Influencia de los accesorios y conectores en el comportamiento durante la refrigeración del molde
04.2021 | 8 min
By Csaba Csipke
Introducción
¿Prestamos suficiente atención al proceso de atemperamiento?
Aunque el atemperamiento desempeña un papel importante en la tecnología de moldeo por inyección, la cantidad de sistemas de monitorización de este proceso en las plantas de producción es insignificante. Las compañías de moldeo por inyección suelen confiar en los datos de máquina durante los procesoa de inyección y atemperamiento. En la mayoría de los casos, el atemperado del molde se basa en la información del controlador sin un proceso de validación. Para entender el proceso, no basta con confiar en los datos mostrados en el controlador. La temperatura de la superficie del molde (zona donde se conforma la pieza) y la temperatura establecida para el agua dependen de muchos factores, por lo que su control y seguimiento se hacen imprescindibles. La diferencia entre los dispositivos de templado, el elevado número de serpentines, la longitud y el tamaño de las mangueras, los conectores utilizados y los colectores pueden aportar un factor de incertidumbre al proceso de templado y, por tanto, modificar el equilibrio térmico del molde.
La vida útil del molde puede ser fácilmente de 5 a 10 años, y durante ese tiempo se requiere mantenimiento. El agua en circulación por el interior del molde a menudo se comporta de forma agresiva con los metales y provoca una corrosión no deseada. La calidad del agua afecta en gran medida a la aparición y al tamaño de los depósitos en los circuitos de agua, los cuales deben pasar por un proceso de limpieza con regularidad. A modo de ejemplo, 1 mm de espesor de cal puede reducir la transferencia de calor en un 6%.
Los sistemas de monitorización ofrecen una solución inmediata para identificar errores imprevistos. de la Con estos sistemas, un conector aflojado, un dispositivo de control no conectado o una manguera conectada de modo inverso, pueden detectarse inmediatamente. Durante la producción en serie, una manguera dañada ciclo a ciclo o la conexión inadecuada de un conector autoblocante pueden provocar grandes cambios en el volumen de agua, siendo su identificación un proceso complejo y que require de mucho tiempo.
Al iniciar la producción con un nuevo molde de inyección, se recomienda registrar no sólo los parámetros inherentes al moldeo en sí, sino también los datos de atemperado. Factores como la disposición del circuito de refrigeración o la identificación del dispositivo de atemperamiento utilizado, así como el volumen y la temperatura del agua pueden garantizar la calidad contínua del producto y un proceso productivo estable.
Además de la temperatura del agua, el caudal desempeña un papel importante en el templado del molde. Sin controlarlo, no podemos estar seguros de que los distintos dispositivos de atemperamiento operen de un modo análogo. En la práctica, pueden surgir diferencias significativas entre los dispositivos de atemperamiento a lo largo del tiempo. La supervisión periódica del estado de la bomba es una solución para comprobarlo. También se recomienda realizar mediciones después del mantenimiento del molde para verificar su permeabilidad al agua.
A través de nuestro sistema de monitorización queremos mostrar la importancia de establecer y mantener un entorno de atemperamiento adecuado y monitorizarlo de modo contínuo. A menudo pueden producirse diferencias significativas entre dos dispositivos de atemperado idénticos, que analizaremos y sobre las que evaluaremos su efecto en la reducción en el caudal. El control de atemperamiento ofrece una solución para detectar errores, como el cambio del estado del dispositivo de atemperamiento, una manguera mal conectada o incluso a un ajuste inadecuado. Estos cambios son poco o nada detectables sin el sistema de monitorización.
Materiales y equipos empleados
Dispositivo de atemperamiento:
Durante la medida utilizamos dos dispositivos de atemperamiento idénticos, modelo Wittmann Tempro Basic C91 (Tabla 1). Su año de fabricación es el mismo, pero su tiempo de operación es diferente, por lo que su eficiencia también será distinta. La temperatura de funcionamiento de los dispositivos de atemperamiento es de 35°C.
Tabla 1. Principales datos técnicos del dispositivo de atemperamiento Wittman Tempro Basic C90
Potencia de calefactado |
kW |
9 |
Capacidad de bombeo |
l/min, |
40 |
bar |
3,8 |
|
Conexiones de agua de refrigeración |
Col |
1/4 |
Conexión de entrada |
Col |
3/4 |
Conexión de retorno |
Col |
1/2 |
Conexionado eléctrico |
V, Hz |
3 x 400, 50 |
Volúmenes de llenado |
l |
9 |
Volúmenes de purga |
l |
3 |
Dimensiones |
mm |
|
Ancho x |
235 |
|
Altura x |
660 |
|
Profundidad |
590 |
|
Peso en vacío |
kg |
31 |
Sistema de medida:
Para el registro de datos utilizamos el sistema de monitorización de caudal de agua de Cavity Eye, con el que controlamos continuamente los valores de caudal y presión, instalando un sensor en el circuito.
Accesorios en el circuito
Los conectores rápidos y los racores utilizados para las mediciones fueron suministrados por Meusburger Hungary Kft. (Tabla 2).
Tabla 2. Conectores de agua tipo Meusburger empleados para las mediciones
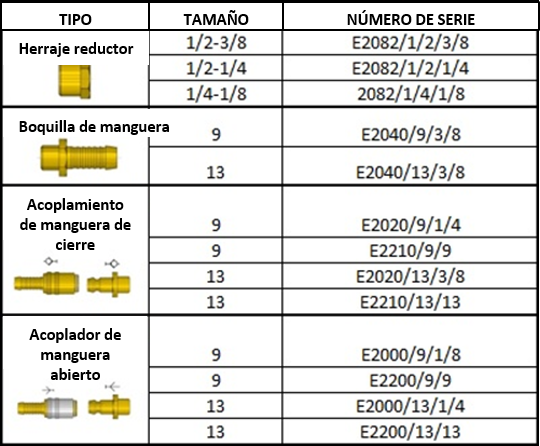
Planificación / presentación del experimento
Configuración de la cadena de medida
Durante la medida, los dos dispositivos de atemperamiento fueron equipados con un sistema de medición idéntico, que controlaba los datos de los circuitos de agua del lado del molde. El sensor forma parte del sistema y está instalado tras un tramo de tubería de 850 mm de longitud. En el extremo de un tramo de tubería de 400 mm de longitud se instalaron los conectores rápidos y la válvula de mariposa. En los experimentos se comprobó el efecto de los distintos tipos de conectores rápidos sobre el caudal, por lo que sólo se cambiaron éstos para la configuración de las mediciones (figura 1). Trabajamos con dos familias de conectores rápidos con diferentes diámetros (9 y 13 mm), y para la realización de las medidas se modificó el diámetro de las tuberías junto con todos los conectores. El tipo de los conectores de agua utilizados no cambió, sólo su tamaño.

Figura 1. Configuración de la cadena de medida
Durante las pruebas examinamos los valores máximos de caudal y presión en función de los diferentes métodos de conexión y accesorios (Tabla 3). Realizamos medidas comenzando por el diseño más simple de boquilla de manguera hasta los acoplamientos de la manguera de cierre. La forma más sencilla de describir la característica de la capacidad de bombeo de una unidad de atemperamiento es a través de los valores de presión medidos en función del caudal. Para registrar la curva de caudal, utilizamos una válvula que reduce la sección transversal del flujo. Cerrando gradualmente la válvula, obtenemos la presión del agua que fluye en el sistema para un caudal determinado.
Tabla 3. Configuraciones empleadas durante la medición
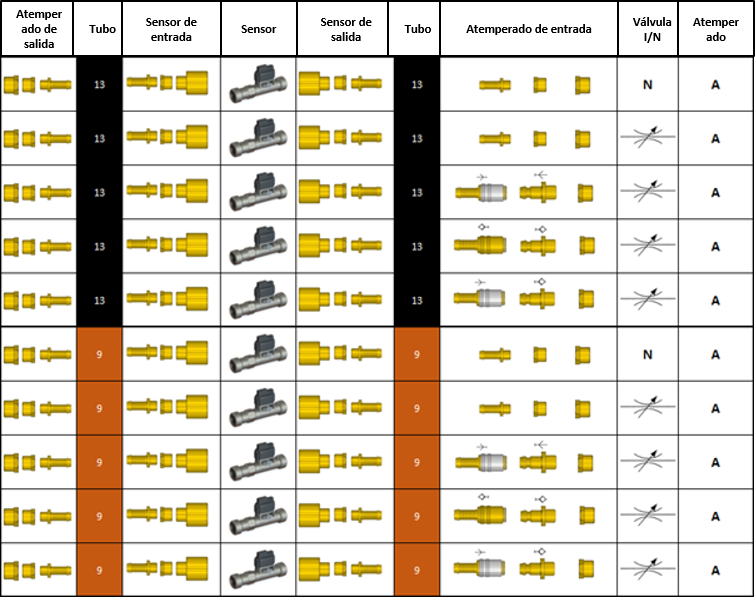
Resultados de las medidas
Efecto de diferentes diámetros de tubería en las características de la bomba
En primer lugar, analizaremos el efecto de los distintos diámetros de las tuberías sobre los valores de caudal y presión en el caso del dispositivo de templado "A". Utilizamos mangueras y accesorios de 9 y 13 mm de diámetro. Se apreciaron diferencias significativas en los flujos obtenidos. (Figura 2.).
Conectando el tubo de entrada y el de salida, sin estrangulamiento cuando se utiliza el tubo de 13 mm de diámetro el caudal fue casi un 40% superior que cuando se empleó el tubo de 9 mm de diámetro. Con el aumento de la presión, las diferencias entre los caudales medidos con tubos de diferentes geometrías disminuyen. A baja presión (1,6 bar), con el tubo de 13 mm se obtuvo un caudal de 16,25 l/min, mientras que con el tubo de 9 mm fue de 9,5 l/min. Esto supone una disminución de más del 40% relacionada con el diámetro de la tubería. Con el aumento de la presión (1,9 bar) la diferencia disminuyó, en el caso del tubo de 13 mm el valor medido fue de 9,75 l/min, mientras que fué de 6,75 l/min para el tubo de 9 mm lo cual significa sólo una diferencia del 30%. En el mismo entorno de templado y en un molde con gran permeabilidad, al cambiar los accesorios de las tuberías y las mangueras, habrá mayores diferencias en el caudal que en un sistema de refrigeración con una permeabilidad pequeña.
Al comparar las tuberías con diferentes diámetros interiores se concluyó que, debido a la mayor sección transversal, se produce una menor pérdida de presión en la tubería de 13 mm de diámetro. Con la misma longitud de tubería, en el sistema de 13 mm sin estrangulador se midió una presión de 1,55 bar, y de 1,24 bar al utilizar los accesorios de 9 mm. Esto significa una caída de presión del 25%, que en el circuito de refrigeración del molde podría aumentar aún más. Por lo tanto, la elección del diámetro de la tubería puede influir no sólo en la eficacia de la refrigeración del molde, sino en la vida útil del dispositivo de templado y en su consumo de energía.
Figura 2. Efecto para diferentes dispositivos de atemperamiento y geometrías de tubo
Se compararon las características de dos dispositivos de atemperado aparentemente idénticos en diferentes condiciones, utilizando tanto el tubo de 9 mm como el de 13 mm. Se observaron diferencias significativas entre los dos dispositivos (Figura 2.).
En la primera fase de la medida, se comparó la capacidad de bombeo de los dispositivos sin estrangulamiento utilizando la tubería de 9 mm y luego la de 13 mm de diámetro. El dispositivo de atemperado "B" fue capaz de producir un 5% más de caudal para ambos tamaños de tubería en comparación con el dispositivo "A". En todo el rango, el dispositivo de atemperado "B" fue capaz de generar un 15-20% más de presión. Por lo tanto, el control continuo de las condiciones de los dispositivos de atemperado es importante, y midiendo regularmente la variación de parámetros podremos saber si el estado del dispositivo de atemperado se está deteriorando drásticamente. Además, con el sistema de control debido a los diferentes valores de flujo se puede detectar inmediatamente si los dispositivos de atemperado fueron intercambiados, evitando incertidumbre en el proceso productivo, así como la aparición de defectos en producción.
Al emplear el tubo de 9 mm de diámetro, a una presión de 1,4 bares en el dispositivo de atemperado "B" se midió un caudal de 13,5 l/min, mientras que a la misma presión en el dispositivo "A" fue de 11,25 l/min. La diferencia entre el caudal de los dos dispositivos de templado es del 17% para la misma presión y diámetro de tubo. Al aumentar la presión a 2 bares, esta diferencia se incrementó al 37,5%. Mientras que en el dispositivo de atemperado "B" se midió un caudal de 10 l/min, en el otro el valor medido fué de 6,75 l/min.
En el caso de la manguera de 13 mm, a 1,7 bar de presión el dispositivo de atemperado "B" garantizaba un 25% más de caudal que el "A". Por lo tanto, en el dispositivo de templado supuestamente más deteriorado se midió un caudal de 14 l/min, mientras que en el dispositivo en mejores condiciones este valor fue de 18,5 l/min. Incrementando la presión a 2 bares la diferencia aumentó al 61,5%. El dispositivo de templado "A" garantizó un caudal de 8 l/min, mientras que el "B" suministró 13 l/min de líquido, lo que puede llevar a modificar por completo el equilibrio térmico del molde. Al aumentar la presión, las diferencias entre los dispositivos de atemperado se hacen más evidentes. Examinando dos dispositivos de atemperado aparentemente idénticos, independientemente del diámetro de la tubería, se observa que uno es capaz de suministrar un 40% más de agua que el otro para el mismo tiempo.
Si en un molde con circuitos de refrigeración complejos y de pequeño diámetro, el mantenimiento del flujo de líquido requiere de un esfuerzo superior, las diferencias entre los dispositivos de templado aumentan. En estos casos, es aún más importante utilizar un dispositivo de atemperado en condiciones adecuadas.
Efecto de los accesorios conectados
Pueden existir diferencias significativas entre las posibilidades de conexión de los tubos con diferentes tamaños y diseños. Los analizamos con diámetros de 9 mm (tabla 4) y 13 mm (tabla 5). Comparamos las boquillas de manguera y los conectores rápidos más sencillos en función del caudal de agua y la presión acumulada. El intercambio de los conectores no provocó un cambio significativo en la relación de las propiedades de la bomba, por lo que comparamos solo los valores de flujo y presión.
Tabla 4. Resultados de las mediciones de los accesorios de 9 mm
Caso |
Caudal |
Disminución del caudal |
Presión |
Cambio de presión |
Herraje reductor |
12,71 |
100% |
1,24 |
100% |
Boquilla de manguera |
11,82 |
93% |
1,30 |
105% |
Acoplamiento de manguera abierto |
9,40 |
74% |
1,59 |
128% |
Acoplamiento de la manguera de cierre |
6,00 |
47% |
2,17 |
175% |
La dispersión de los resultados fue de 0,02 bar y 0,1 l/min. |
En el caso de la manguera de 13 mm sin el uso de conectores rápidos, el caudal obtenido fué de 17,73 l/min. El uso del acoplador de manguera abierto redujo mínimamente el caudal obtenible, variando el valor de presión. La aplicación del acoplador de manguera de cierre facilita el bloqueo automático de los circuitos de agua no utilizados y la prevención de fugas, pero reduce el caudal en un 20% (Figura 4). Si hay una conexión defectuosa (piezas autoblocantes y no autoblocantes), el caudal alcanzable disminuye aún más, incluso hasta el 76% del valor original sin los conectores rápidos.
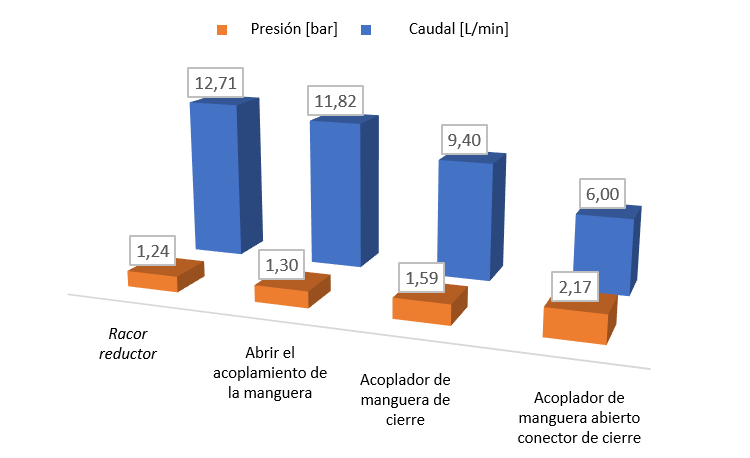
Figura 3. Comparación del ajuste de 9 mm
Con el uso de los accesorios de menor diámetro (9 mm), el efecto limitador del caudal de los conectores rápidos es más significativo que en los accesorios de 13 mm (figura 3). Cuando se utiliza el acoplador de manguera de cierre, la diferencia medida es del 20% en las tuberías de 13 mm, y del 26% en los accesorios de 9 mm. Una conexión defectuosa (conector de cierre del acoplador de manguera abierto) puede dar lugar a un 50% menos de caudal en un sistema de 9 mm, lo que puede provocar incluso un cambio de presión del 75%.
Tabla 5. Resultados medidos con accesorios de 13 mm
Caso |
Caudal |
Disminución del caudal |
Presión |
Cambio de presión |
Herraje reductor |
17,73 |
100% |
1,56 |
100% |
Boquilla de manguera |
17,53 |
99% |
1,53 |
98% |
Acoplamiento de manguera abierto |
14,25 |
80% |
1,69 |
108% |
Acoplamiento de la manguera de cierre |
13,51 |
76% |
1,73 |
110% |
La dispersión de los resultados fue de 0,02 bar y 0,1 l/min. |
Independientemente del tamaño, el acoplador de manguera fue el que menos redujo el caudal, mientras que los conectores rápidos mal empleados fueron los que más afectaron al sistema. Es importante mencionar que un racor de 9 mm mal conectado puede reducir el caudal a la mitad.
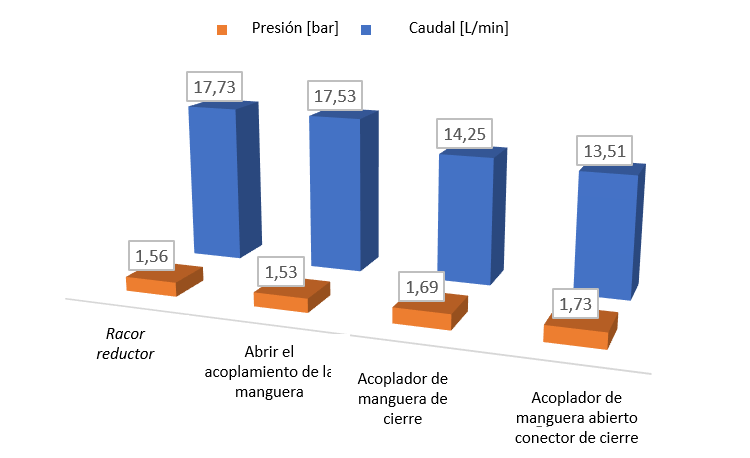
Figura 4. Comparación de los accesorios de 13 mm
Resumen
A modo de resumen de los resultados, dos dispositivos de templado del mismo tipo no son capaces de suministrar el mismo caudal y controlar la temperatura, lo que puede modoficar el proceso por completo. Para alcanzar el caudal adecuado, es esencial elegir la tubería con el diámetro correcto. Al utilizar los tubos de 13 y 9 mm, la diferencia entre los valores de caudal medidos fue de alrededor del 40%.
Además del diámetro, es importante aplicar los racores adecuados, debido a su efecto significativo en el caudal. Con los racores autoblocantes se observó una reducción del caudal de 3 l/min en ambos diámetros. Esta disminución fue del 20% en el caso de los racores de 13 m, mientras que fue del 26% en los de 9 mm.
El atemperado es un proceso complejo, ya que no basta con elegir la combinación óptima de elementos, sino que deben emplearse correctamente. En caso de conexiones defectuosas (acoplador de manguera abierto con conector de cierre) se produce una pérdida significativa, que puede resultar en algunos casos en más del 50% de reducción del caudal. Al inicio de la producción, el tiempo de los operarios de máquina es limitado y los errores de atemperado son difíciles de detectar antes del inicio de la producción. El sistema de medición de flujo de agua de Cavity Eye es capaz de detectar inmediatamente las diferencias, evitando así el inicio incorrecto de la producción o la fabricación de productos defectuosos.
Csaba Csipke
Cavity Eye Hungary Kft - Ingeniero de proyectos