La medida de viscosidad del plástico en la práctica – Parte 3.
05.2021| 4 min
By Szabolcs Horváth
Objetivo de la medida:
Familiarizar a los operarios e ingenieros de máquina con este método, de forma que sean capaces de determinar la viscosidad del material en función de la temperatura y velocidad empleando la máquina de moldeo por inyección.
Introducción
En la primera parte, presentamos el desarrollo teórico de estas medidas, la segunda parte trata acerca del proceso de medida. En la tercera parte, se resumen los resultados de las medidas y las conclusiones.
Evaluación de los datos medidos
El efecto de la geometría de la boquilla en la viscosidad
Con las tasas de inyección previamente establecidas, realizamos la medición con boquillas de diferentes tamaños. Examinamos el efecto de la geometría de la boquilla a una temperatura constante de 285°C.
Tabla 3: Presión requerida para la inyección en función de la velocidad de inyección y de la geometría de la boquilla
Vfrcs |
Boquilla de |
Boquilla de |
Boquilla de |
1 |
200,00 |
212,00 |
210,00 |
2 |
230,00 |
250,00 |
260,00 |
5 |
275,00 |
285,00 |
312,00 |
8 |
315,00 |
335,00 |
370,00 |
10 |
340,00 |
380,00 |
425,00 |
La presión necesaria para la inyección se muestra en función de la velocidad de inyección (Figura 9). Como era de esperar, el aumento de la longitud de la boquilla supuso un incremento en la presión necesaria para la inyección. El incremento de la presión es debido a dos factores, uno es el aumento debido a la geometría (orificio más largo) y otro es el efecto de la temperatura. La parte final de la boquilla no suele calentarse. En algunos casos, se producen problemas de estabilidad durante la producción si la boquilla sustituída en la máquina es más larga que la original y se reanuda la producción con los mismos ajustes y la misma capacidad de calentamiento. Un incremento significativo de la longitud de la boquilla conlleva la necesidad de corregir el tamaño y la capacidad de calentamiento. Durante esta medición se validó la distribución de la temperatura a lo largo de la longitud de la boquilla con un termopar, por lo que sólo se puede evaluar el efecto de la geometría.
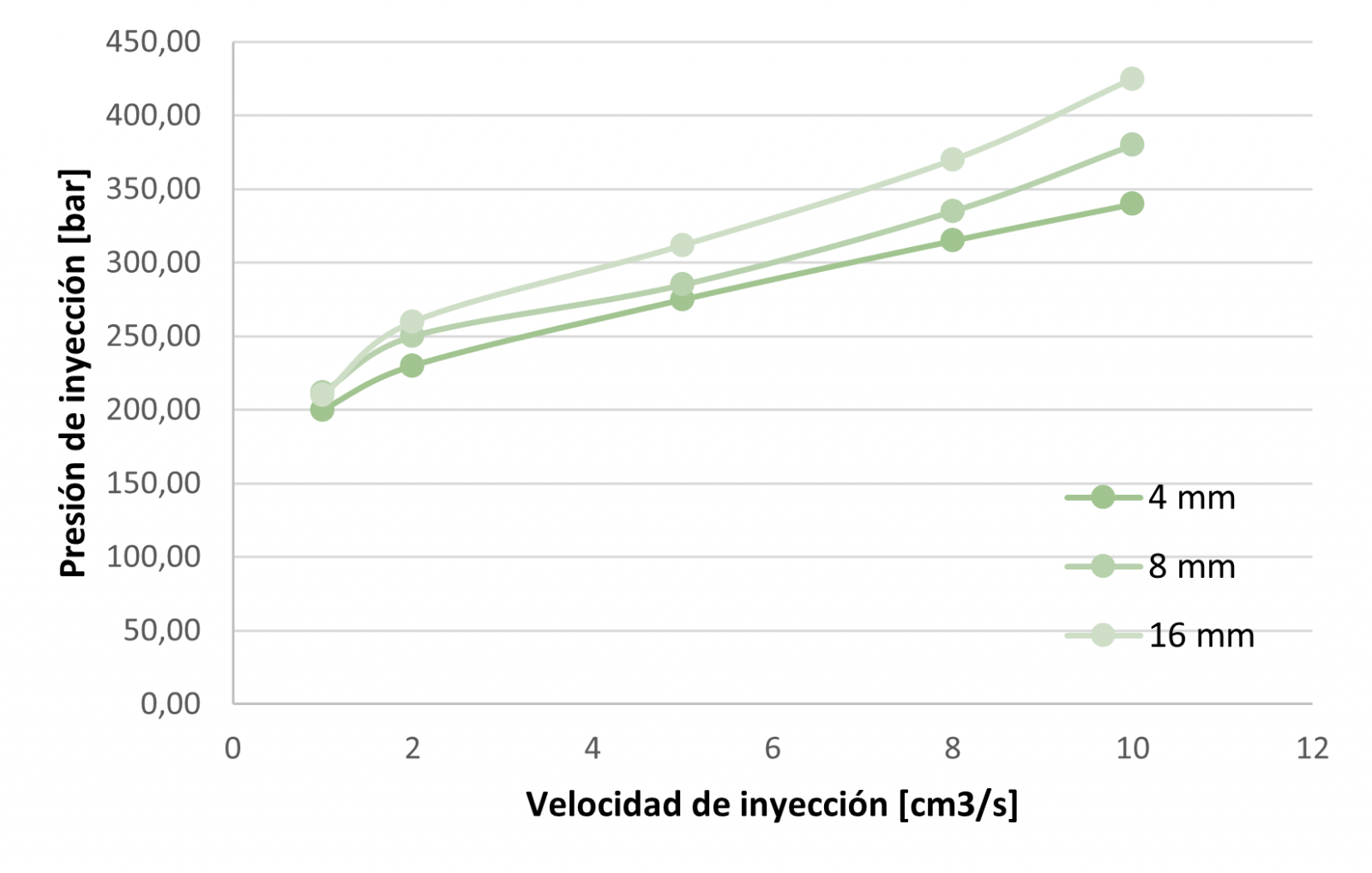
Figura 9: Presión necesaria para la inyección en función de la velocidad de inyección, material PA66, temperatura del material de 285°C
El aumento de la longitud de la boquilla dio lugar a la disminución de la tensión de cizalladura aparente. Las moléculas se asientan en la dirección del flujo y debido a la orientación su resistencia al avance disminuye, por lo que el esfuerzo cortante aparente también será decreciente. Es importante tener en cuenta que el esfuerzo de cizalladura aparente está relacionado con la geometría de la boquilla dada, por lo que el requerimiento de presión para la inyección aumentará más cuanto más larga sea la boquilla que utilicemos, sin embargo el material sufrirá un menor esfuerzo de cizalladura.
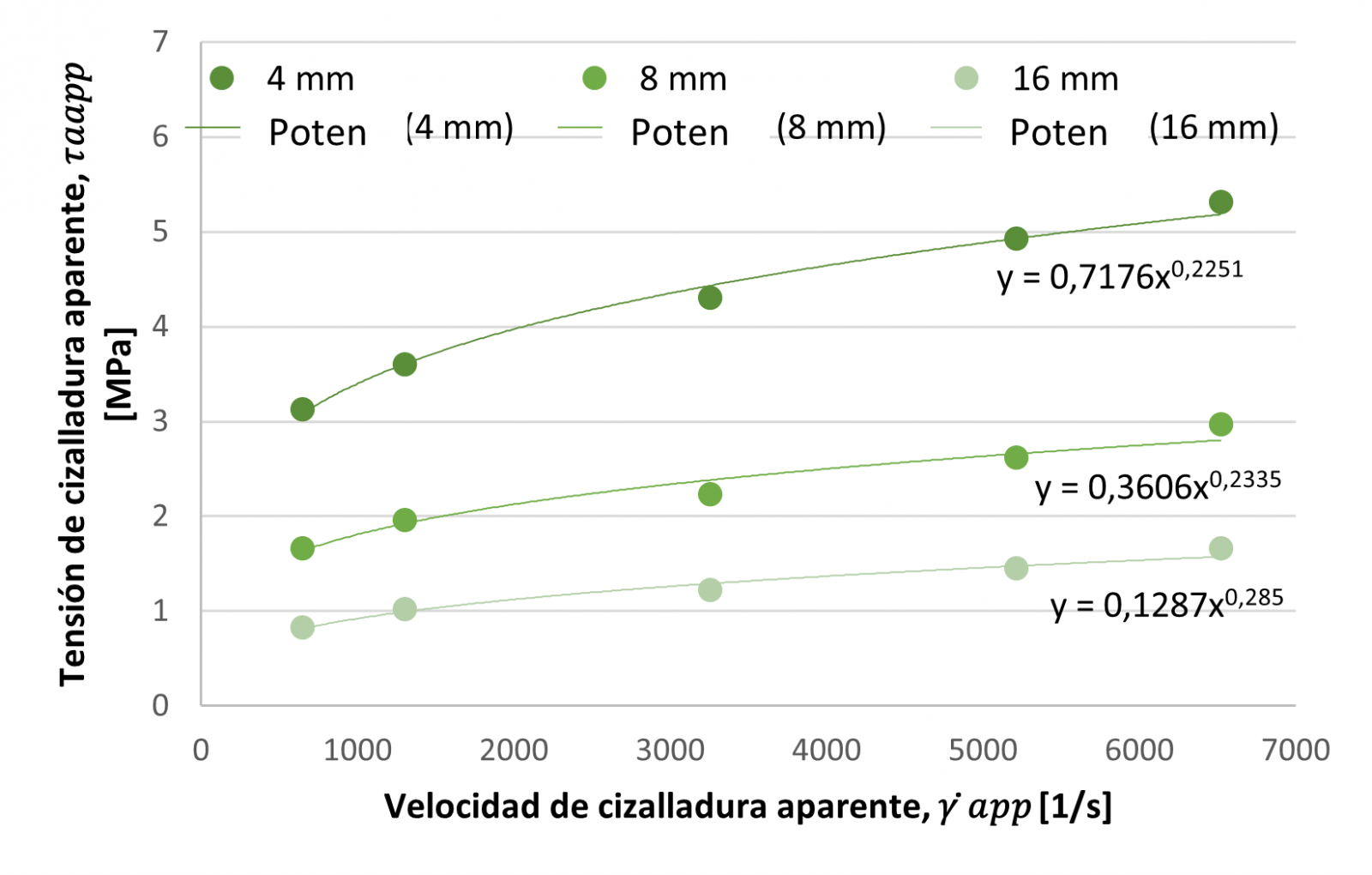
Figura 10: Esfuerzo de cizalladura aparente en función de la velocidad de cizalladura aparente, material PA66, temperatura del material de 285°C
Incrementando la longitud de la boquilla se produce una disminución de la viscosidad a una temperatura del material de 285°C. Cabe destacar la diferencia entre cada boquilla en función de la velocidad de inyección. A una velocidad de inyección baja (650 1/s - 1cm3/s) con una boquilla de 4 mm de diámetro la viscosidad medida es de 4800 Pa*s, mientras que con la boquilla de 16 mm este valor es sólo de 1200 Pa*s. La razón es que las moléculas están más organizadas al tratarse de un corredor más largo y la resistencia al flujo será menor. Al aumentar la velocidad de inyección, la viscosidad se vuelve menos dependiente de la geometría de la boquilla. Las diferencias serán menores entre las boquillas individuales. A 6500 1/s (10 cm3/s) de velocidad de deformación aparente, la diferencia entre los valores medidos es inferior a 600 Pa*s.
El aumento de la velocidad de inyección ayuda a minimizar las diferencias causadas por la diferente geometría de las boquillas y a reducir su efecto en el proceso.
Figura 11. Viscosidad aparente en función de la velocidad de cizalladura aparente, material PA66, temperatura del material de 285°C
Resumen
La medición de la viscosidad puede realizarse fácil y rápidamente en una máquina de moldeo por inyección tradicional en pocos pasos. La medición permite comparar las diferentes materias primas y las propiedades de los mismos materiales que se han fabricado bajo diferentes series de producción.
Uno de los factores de mayor variabilidad durante el proceso de moldeo por inyección son las propiedades físicas, mecánicas y estructurales del polímero empleado. Con el método de medición de la viscosidad se pueden realizar comprobaciones y verificaciones con datos, simplificando así la resolución de problemas en el proceso de moldeo por inyección. El cambio de temperatura o el uso de una boquilla inadecuada tiene un efecto significativo en todo el proceso de producción. Basándose en las medidas obtenidas, con el aumento de la velocidad se pueden reducir en gran medida las diferencias causadas por la temperatura y la geometría de la boquilla.